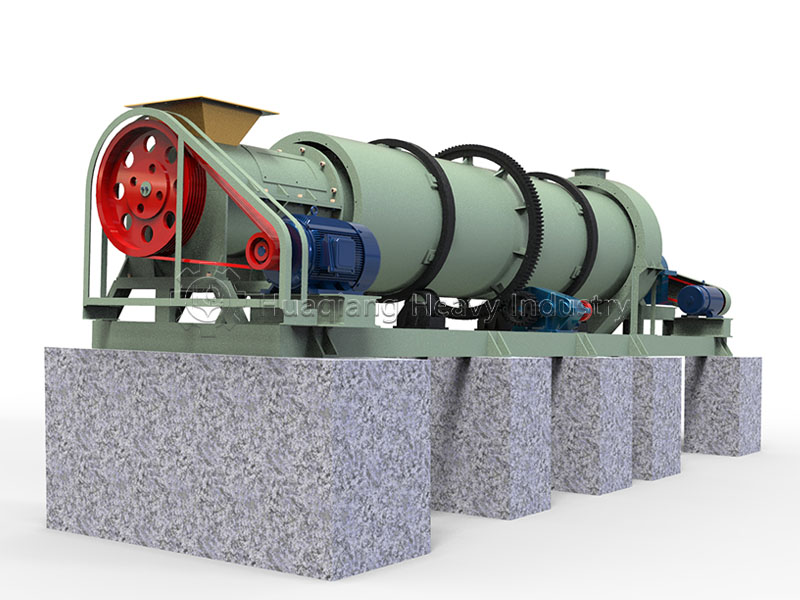
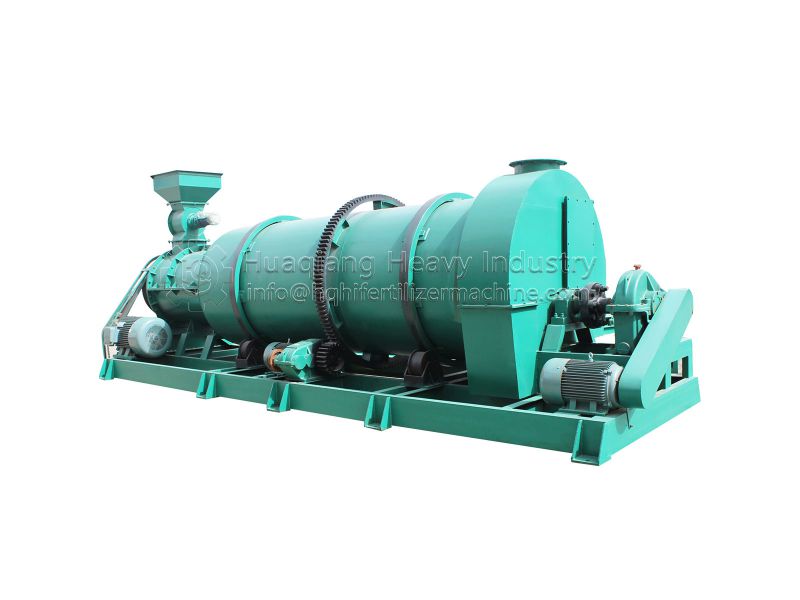
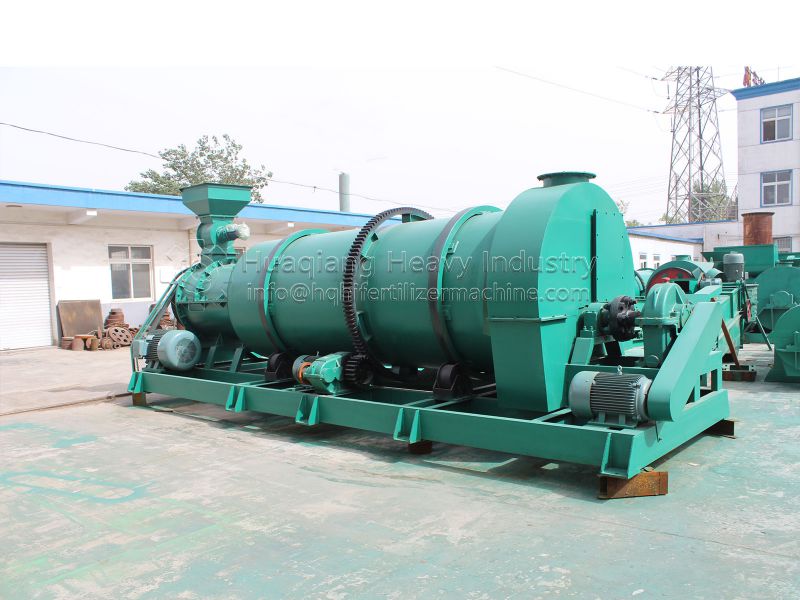
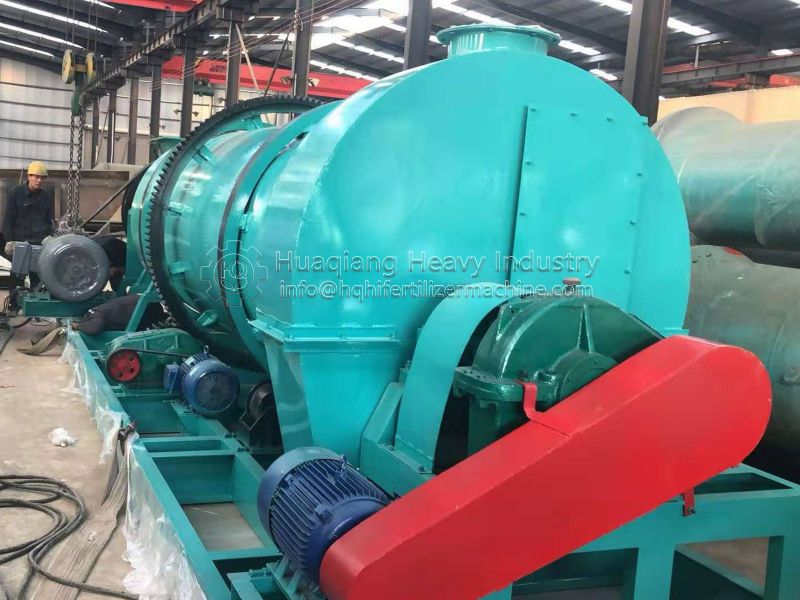
New Type Two In One Organic Fertilizer Granulator
The new type of stirring tooth organic fertilizer granulator is an advanced equipment specially designed for organic fertilizer granulation. It combines the dual functions of stirring and granulation, and can efficiently convert organic materials into uniform granular fertilizers. It is particularly suitable for treating various organic wastes, such as livestock manure, crop straw, urban sludge, etc. Compared with traditional organic fertilizer granulators, the new toothed organic fertilizer granulator has significantly improved granulation efficiency, particle quality, and operational convenience.
Scope Of Application
The new toothed organic fertilizer granulator is suitable for granulating various organic materials, including but not limited to:
Livestock and poultry manure: chicken manure, cow manure, pig manure, etc.
Crop waste: straw, rice husk, soybean meal, etc.
Urban organic waste: kitchen waste, garden waste, urban sludge, etc.
Industrial organic waste: by-products of food processing, paper waste, etc.
Equipment Structure And Composition
The structure of a new type of agitator for organic fertilizer granulation usually includes the following key components:
Mixing and granulation drum: equipped with specially designed mixing teeth inside, used for mixing and granulation materials.
Transmission system: Provides power to drive the rotation of the teeth and cylinder.
Feeding device: Ensure that the material is evenly and continuously fed into the granulation drum.
Discharge outlet: The outlet for finished particles.
Control system: used to monitor and adjust key parameters during the granulation process, such as temperature, humidity, and stirring speed.
Cooling and drying system: Ensure that the particles after granulation can be quickly cooled and dried to improve the stability and hardness of the particles.
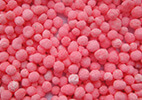
Working Principle
Material pretreatment: Firstly, organic materials need to be crushed and pre mixed to ensure uniformity and appropriate particle size. At the same time, adjust the humidity of the material as needed to achieve the required humidity level for granulation, usually between 30% -40%, to improve the plasticity and adhesion of the material.
Feeding and mixing: The pre treated material is evenly fed into the mixing and granulation drum of the toothed granulator through the feeding device. The cylinder is equipped with specially designed stirring teeth, and the rotation of the stirring teeth can fully stir and mix the materials, promoting the uniform distribution of materials and the initial formation of particles.
Plastic deformation and granulation: In the mixing and granulation drum, the rotation of the stirring teeth and the interaction between the materials cause plastic deformation of the materials under specific humidity and pressure conditions. Through extrusion and bonding, the materials gradually form particles. This process is usually accompanied by an increase in the temperature of the material, which helps to improve the stability of the particles.
Cooling and drying: After granulation, organic fertilizer particles usually need to be rapidly cooled through a cooling system to stabilize the particle structure and prevent deformation or adhesion due to high temperature. After cooling, the particles need to be dried to remove excess moisture, improve their hardness and stability, and facilitate storage and transportation.
Screening and post-processing: Finally, the cooled and dried particles are passed through a screening device to remove unqualified particles (such as oversized or undersized particles). Qualified particles after screening can be packaged or further processed as needed, such as adding nutrients, microorganisms, etc.
Equipment Features
Efficient granulation: Through the special design of the stirring teeth, it is possible to achieve rapid and uniform mixing of materials and efficient granulation, resulting in high granulation efficiency.
Good particle quality: The organic fertilizer particles after granulation are uniform, moderately hard, and have good solubility, which can meet the nutritional needs of crops.
Wide applicability: capable of handling various organic materials, including high humidity and viscous materials, with a wide range of applicability.
Simple operation: high degree of automation, easy operation, and convenient maintenance.
Environmental protection and energy conservation: The granulation process produces low dust and noise, low energy consumption, and meets environmental protection requirements.
Compact structure: Compact design, small footprint, suitable for production needs of different scales.
Have Any Problem? Please, Contact
Integrity
Adhere to honesty and trustworthiness, be responsible to customers, employees, partners, and society, and establish long-term trust relationships.
Win win
Establish win-win relationships with all stakeholders such as customers, suppliers, and employees to share the fruits of enterprise development.